Winter 2012 Forum
HOW MUCH OF YOUR HEAT IS GOING UP THE CHIMNEY?
Heat Recovery…Making Your Heat Work For You
December 12, 2012
Portland State University - Native American Student Community Center, Portland
Oregon APEM’s Winter Forum was held at Portland State University’s Native American Student Community Center in downtown Portland. This building is a place for learning that was specifically constructed to serve the Native American, Alaskan Native and Pacific Islander students at PSU; fortunately, this building is also available for other community gatherings and educational events. This beautiful building was constructed with several energy conserving strategies including maximized building orientation for solar energy gain, natural daylighting, a rooftop solar array and a rooftop garden that reduces stormwater runoff. The building also features natural ventilation without mechanical assistance.
The Winter Forum was the final forum of 2012; this is significant because it was 30 years ago that the APEM organization came into existence. We celebrated our 30th anniversary by beginning the day with a discussion of some of the noteworthy events of 1982 and some of the significant changes between now and then. The Oregon APEM board would like to take this opportunity to thank all the members, speakers and board members who have helped develop and sustain the Oregon APEM organization.
Our first speakers of the day were Tim Elley and Nedzib Biberic from PAE Consulting Engineers. Tim and Nedzib began with an explanation of the fundamentals of heat recovery. They explained how heat can be recovered from and transferred to various mediums in different situations. For example, heat can be recovered:
• From water, like regaining heat from grey water to preheat non-potable or domestic water or like using a run around loop to preheat supply air;
• From air to air, like transferring heat from exhaust air to supply air using flat plate, heat wheel, heat pipe or energy core heat exchangers;
• From the earth, by using ground source heat pumps or geothermal hot water;
• From one space to another space in the same building by a variable refrigerant flow system or heat recovery chiller;
• Or from a building to another building by use of underground piping which connects buildings with different load profiles.
Tim and Nedzib discussed the Oregon Zoo which uses underground piping to move heat around its entire campus. They explained, for example, how the polar bear and seal areas need constant cooling while the primate and elephant areas need near constant heating; the heat removed from one area can be transferred to other areas, greatly reducing the energy usage of the Zoo campus.
Next, Tim and Nedzib talked about some situations where heat recovery should be considered. Firstly, they reminded is that there are many cases where the Oregon Energy Code currently requires heat recovery to be installed. Secondly, they discussed how the energy end uses of a building need to be analyzed before heat recovery is installed. Buildings with high heating and cooling loads can be good candidates for heat recovery and different types of heat recovery will make sense for different types of buildings. Third, they recommend that a Life Cycle Cost Analysis is completed to determine the potential cost savings of a specific project. Finally, Tim and Nedzib shared some examples of heat recovery in action at the Port of Portland Headquarters building and at Chemeketa Community College. See Their Presentation
Our next speaker was Doug Hansberry a Professional Engineer who has been working to optimize Intel’s fabrication plants for the last 17 years. Doug’s presentation focused on heat recovery chillers which are used extensively in Intel’s new fabrication plants. Doug started off with a demystifying explanation of how a heat recovery chiller works. A traditional chiller has two sections, the condenser and the evaporator sections. Refrigerant is used to remove heat from the chilled water loop and transfer it to the condenser water loop. The condenser water loop moves the heat to the cooling tower where the heat is rejected to the atmosphere. In a heat recovery chiller, there is a third section, the heat recovery condenser. The chiller is optimized to create 90-105 degree heating water instead of rejecting the heat to the atmosphere through the cooling tower. The potential heat available in the heat recovery condenser water loop is the sum of the heat removed from the chilled water loop plus the compressor waste heat. This available heat can greatly reduce or even eliminate the need to heat a low temperature hot water loop with a boiler, when the chiller is operating.
Heat recovery chillers do pay a slight energy penalty by having a lower cooling efficiency than traditional chillers, for instance a heat recovery chiller will have a 0.56 kW/ton efficiency whereas a cooling only chiller will have a 0.52 kW/ton efficiency at the same operating conditions. Operating the heat recovery condenser water loop at the lowest possible chilled water temperature can help to minimize this efficiency difference. Nevertheless, Doug has found that the cooling penalty that is paid by using a heat recovery chiller can be greatly offset by reduced boiler energy needed for the hot water loop, in the right application.
Heat recovery chillers have a higher initial cost, and they can only generate hot water up to about 105 degrees. In order to adequately heat a building with 105 degree water you will often need larger coils in the air handlers than you would if the incoming hot water was 180 F, and these larger coils often require more fan power to deliver the air across the coils. You may also need larger sized pipes to than you would if you were using the higher temperature water. These factors also increase the first cost of a new system designed around heat recovery chillers, and lead to slightly higher energy costs for fan power and pump power.
Even though there are some drawbacks to heat recovery chillers (HRCs), they can be very economical and are highly recommended when installed in appropriate situations. Doug explained that the load profile of the building is extremely important to the success of the HRC. These systems work best in buildings with high cooling baseloads all year long. If a chiller only needs to remove heat from the chilled water loop during the summer, then the only time that there is heat in the heat recovery condenser loop is when heating water is least needed. Even with the increased installed costs, Doug reported that Intel has found that in its fabrication plants, the simple payback of this system after incentives is 2.6 years.
There are some additional benefits to heat recovery chillers. When a HRC can offset the need for a fossil-fuel fired boiler then they will greatly reduce the emissions of NOx, CO2 and other air pollutants. Additionally, the water usage of a facility can be greatly reduced because the evaporation of water at the cooling tower is greatly reduced or eliminated. Unfortunately Doug's presentation is unavailable
After a morning full of informative and technical presentations, it was time to announce Oregon APEM’s Energy Manager of the Year award winner. After the other five nominees were recognized, the Energy Manager of the Year award was presented to Cathy Higgins, Research Director at the New Buildings Institute. Cathy gave a presentation about the work that she has been doing at NBI which earned her Oregon APEM’s award for 2012.
Cathy explained how she has spent a career focused on how to collect, compare and communicate data about building energy consumption. She showed us the NBI First View Tool which gives performance indicators to building operators. This tool, along with a multitude of other tools and publications is free for download on the New Buildings Institute’s website. Cathy described her work on technologies and occupants; the sensitivity analysis completed by NBI show the relative impact of design, operation and tenant behavior on the energy use of a building. Techniques to reduce plugloads and lighting loads have been researched and investigated by NBI.
Finally, Cathy highlighted her leadership in the field of Zero Net Energy Buildings which produce as much energy as they consume. In a recently released NBI study, which was the largest of its kind, Cathy and her team analyzed 99 buildings across the country to determine how many are truly Zero Net Energy buildings. The study found that 21 buildings are zero net energy, with the rest being zero net capable or potential. This is the first large study of its kind which was based on documented empirical data. See Her Presentation
The Oregon APEM board would like to congratulate Cathy Higgins and thank her for all of her great work. A summary of the work of each of this year’s Energy Manager of the Year award candidates is available on the Oregon APEM website at www.oregonapem.org.
After Cathy’s presentation, the attendees were turned loose to network and eat lunch before embarking for the building tour. The group took the streetcar to the South Waterfront where we were treated to a tour of the OHSU Center for Health and Healing. This 16 story, 400,000+ square foot building features:
• A biodigester waste processing system
• Natural gas heat and energy cogeneration
• Heat recovery chillers
• Several types of heat recovery including air-to-air and water-to-water
• Radiant floor heat in the lobby
• Natural ventilation in the stairwells
• Chilled beams for passive convective cooling
• Daylighting, daylight dimming, and LEDs
• A solar wall on the south side of the building
• A 60 kW solar panel array on the south side of the building that also serve as window shades
• Solar thermal water heating
• A vegetated roof
• Rainwater harvesting
• A LEED Platinum rating
Presentations:
Tim Elley and Nedzib Biberic, PAE Consulting Engineers
Doug Hansberry
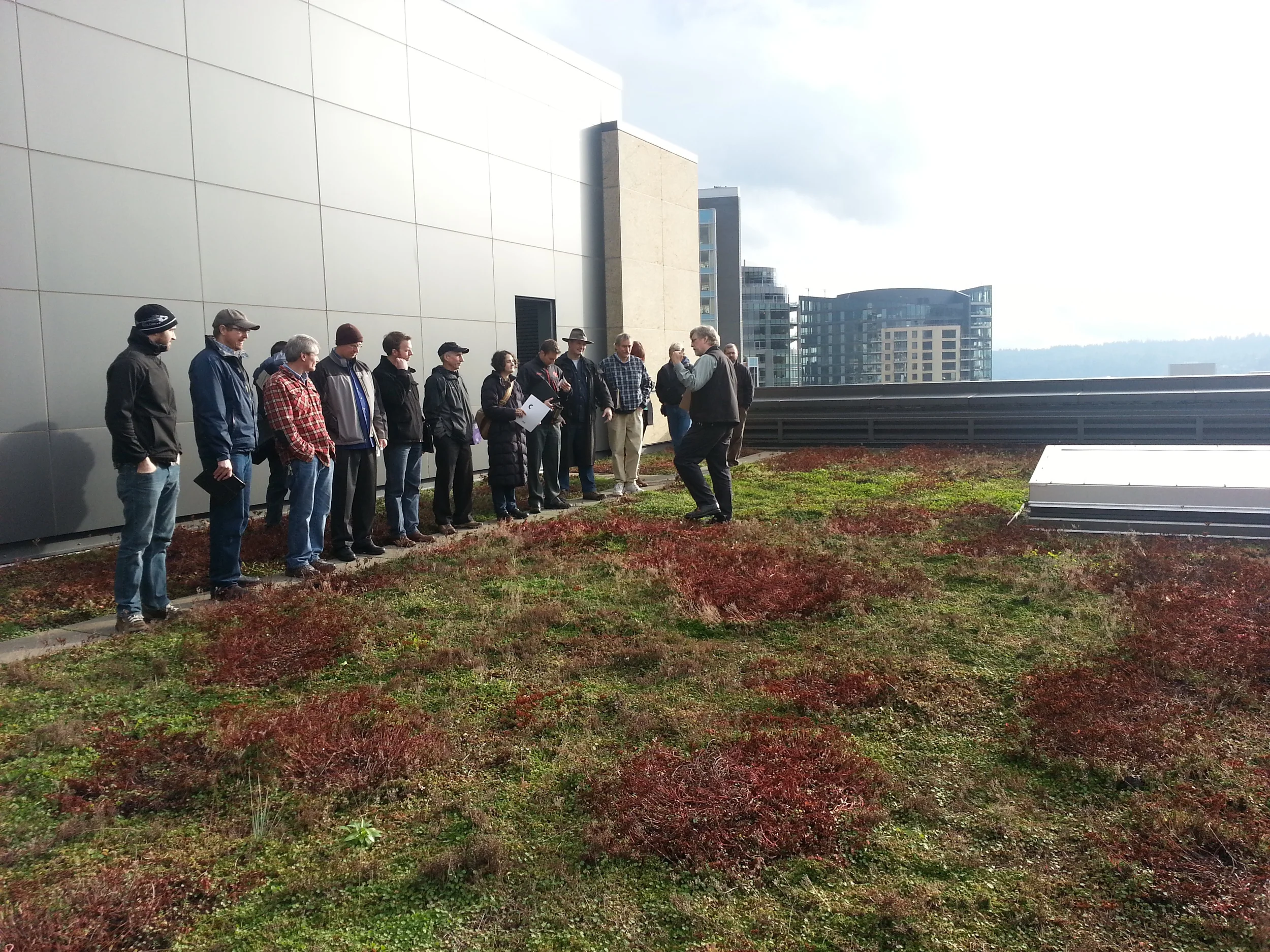